- June 15, 2020
- Category: Automation
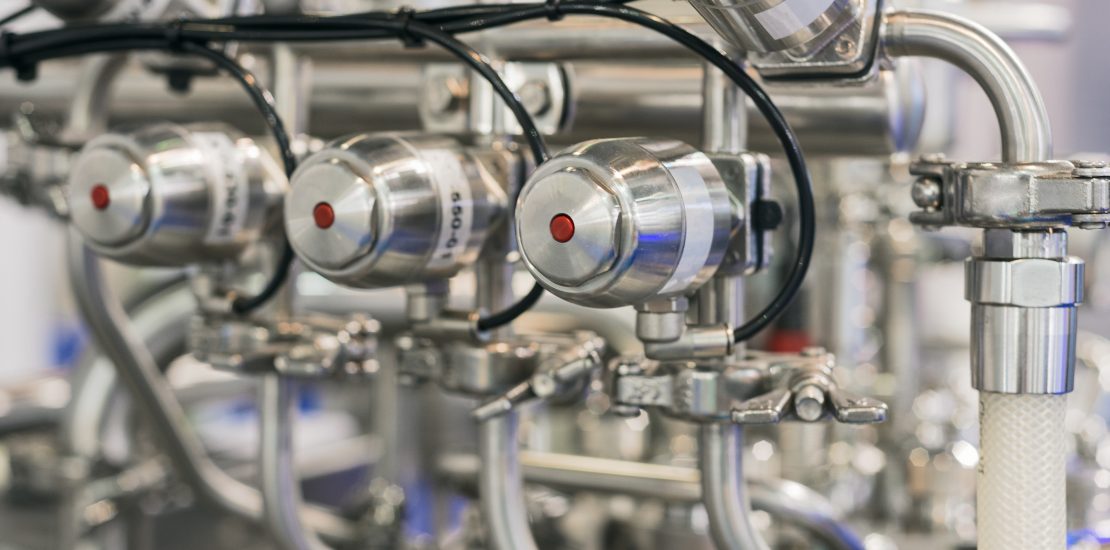
So, your automation system, whatever it might be, is getting old, or at least older. As the saying goes: “I thought getting old would take longer”. Perhaps your current automation system is running smoothly and has gotten past it’s “growing pains” period and paid back it’s ROI many times over. But now replacement parts to keep it fully operational are getting harder to find, and it is not as easy to maintain or find specialists to do so.
This discussion will serve to highlight issues that may arise after you have started the migration process, as well as those issues that are wise to consider during the planning stages. If this is early in the process, you may be looking ahead, perhaps an evaluation is underway, and your team is looking at how smooth or bracing for how bumpy this transition period will be. Of course, it cannot be overestimated how much teaming up with a trusted, experienced partner in this process can ensure things go as smoothly as possible.
Migrating a process automation system provides an opportunity to leverage the benefit of experience to improve on designs and incorporate feature-rich equipment offerings. The typical desktop computer of 15 or 20 years ago was certainly limited in its capacity and ability when compared to the advances in technology that have unfolded in the years since. Automation systems are no exception.
An example of what might drive the migration to a new system is the leveraging a new technology. New systems can make use of network, fieldbus, HART and even wireless technologies.
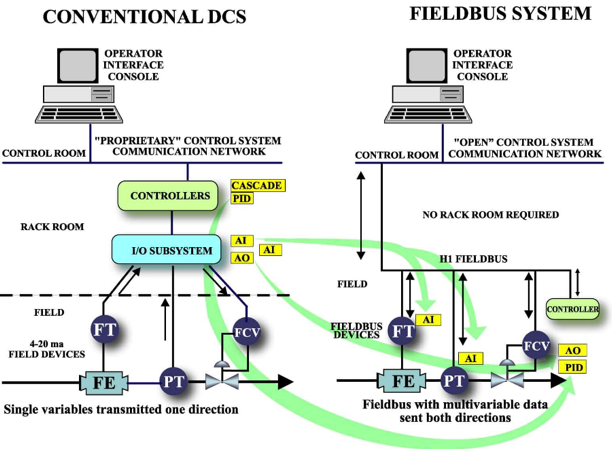
With that said, you will certainly have plenty of challenges as it is without taking on too ambitious of a redesign. There’s a case to be made for a “like for like” transition, thereby ensuring testing can be an “apples for apples” comparison. This also ensures something radically different doesn’t make validation/testing have to undergo its own radical make-over. The new capacities of a modern automation system are impressive, with dramatic improvements in capacity and speed, while benefitting from designed-in enhancements with both ease of use and convenient, intuitive design and configuration utilities.
However, the planning and execution of the necessary engineering tasks is not to be taken lightly, as there is still a considerable body of work to be accomplished. As the old insurance advertisement used to claim: “It’s so easy, a caveman could do it”. Well, maybe so, but that still doesn’t mean you actually want a caveman designing and configuring your new automation system.
The executive offices are abuzz with each new report of a migration project boasting a “zero downtime” execution emanating from vendors’ web pages, but it can overlook that considerable meticulous planning is required ahead of time to make this achievement a reality. And careful advanced planning can ease the pain. There is the inverse relationship between pain vs. budget. Less budget = less time = more pain.
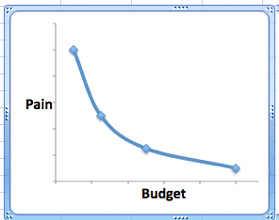
Assessment of Existing System and Infrastructure
At the risk of stating the obvious, a thorough examination of “what is” – starting with some assessment of “wants” vs. “needs”, does the new system address an enhancement in function, or is the goal just avoiding the difficulties associated with obsolescence? Is the primary a “like for like” or is there an expansion, or new function driving the project? This is most often the case – a legacy system might be performing fine but deemed too difficult to expand to accommodate some modification or expansion of the process operations.
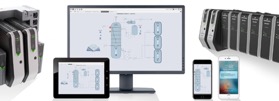
So a map of goals and milestones is paramount, and it establishes a hierarchical view, from the big picture then diving ever deeper into the details. The breakdown will entail the goals and results and how to measure them:
- Plant & Company Level:
- Production throughput increases
- Higher and more consistent quality
- More reliable – automatic, less human monitoring and intervention
- Engineering Level:
- Review and backfill gaps in functional and design specifications
- Plan improvements in
infrastructure:
- Should fiber replace copper runs
- Should key instruments be upgraded, network I/F replace 4-20 ma
- HART capable instruments provide asset management window
- Operations Level:
- New HMI design improves operator effectiveness overall
- More effective anomaly response with enhanced alarm management
- Widely distributed HMI (web
based, wireless) –
- Built in security compliance with CFR11 Part 23.
- Provides engineering, quality and production personnel with more immediate access
Then there follows a detailed analysis of the existing system. This is depends upon the nature and state of existing documentation of the legacy system.
- Survey and Assessment of
existing legacy system being replaced:
- Dump/extract or otherwise
document existing system configuration
- Tag and I/O landing termination, scaling, alarm set points
- Scan or event driven logic/interlocks
- Existing connectivity, serial or Network documented
- HMI graphics/displays, and hierarchy & access documented
- Dump/extract or otherwise
document existing system configuration
The project team now focuses on the replacement strategy planning.
- Physical layout planning
- Cabinet placement and utilities service planning
- Identify where “like for like” fits – same service or other direct replacement fits
- Identify new or altered services, such as a higher power requirement needing an upgraded service.
- Ensure matched electrical
connectivity including all instrumentation wiring.
- Marshalling electrical signals as needed
- Verification of the end to end replacement of signal path
- HMI operator workstations planning, is that 1 for 1, or additional stations need to be planned and documented
- Physical planning system to
environment
- Infrastructure connection
- Signal path planning and firewall impacts
- Logical and Software planning
- Using the data collected
earlier, implement configuration to construct the new system with features and
function in Sync with every observable aspect of the legacy system it replaces.
- Tag and I/O landing termination, scaling, alarm set points
- Scan or event driven logic/interlocks
- Existing connectivity, serial or Network
- HMI graphics displays and HMI hierarchy & access
- Plan login authentication strategy and privilege levels of system access for different system users.
- Plan validation documentation – using previously collected data, generate AIQ and AOQ documents against the requirements and design documents
- Using the data collected
earlier, implement configuration to construct the new system with features and
function in Sync with every observable aspect of the legacy system it replaces.
Now the new system is taking shape and the testing will prove the accuracy of the preceding steps.
- Testing – shakedown
- Testing of all internal signal
paths
- Server – Database access
- Controller connectivity, redundancy and IP rules implemented
- Business network connectivity, if required
- OSI Pi data integrity testing and re-validation (if appropriate)
- Verify all signal paths to I/O devices signal transmission
- Verify scaling is retained as expected for analog points
- Ensure end-to-end signal integrity, such as AI or DI being properly displayed on the HMI screen.
- Ensure signal continuity is maintained throughout the automation systems infrastructure
- Testing of all internal signal
paths
- Formal Validation
- IQ – all installation tasks – signal checkout
- OQ – operational checkout – URS or FRS conformity according to validation testing protocol
- PQ – Performance Qualification testing protocol
With proper planning and preparation, the process can be made virtually pain-free; no tears or sweat needed.
If you partner with an automation service provider, you will want to be sure they have the answers to your questions and planning tools such as:
- What steps will you take to ensure: the migration is “seamless”, operations can continue smoothly upon startup of the new system (operators, systems ready)
- What steps will you take to ensure: no loss of configuration data, control logic and HMI graphic displays.
- How similar/different will the graphic look and operate.
- Provide an outline of the milestones for project progress metrics & customer acceptance criteria of project segments.
- Provide an outline of the project staffing and role and responsibility for customer personnel support of your project staff.
- Provide an outline of the project reporting and assessment criteria. This includes acceptance by customer and follow up warranty for errors or omissions discovered after hand-over.
Automation partners that perform automation system migrations year in and year out are well familiar and able to ensure that your migration is pain free, and frees your personnel up to manage their ongoing responsibilities, without learning new skills and engaging in tasks they’ll use only this once, or once every twenty years at most. Once the migration is complete, you can literally reset the clock on your system, and rest assured that that your infrastructure investment will stand the test of time, until it’s time to do the next upgrade.
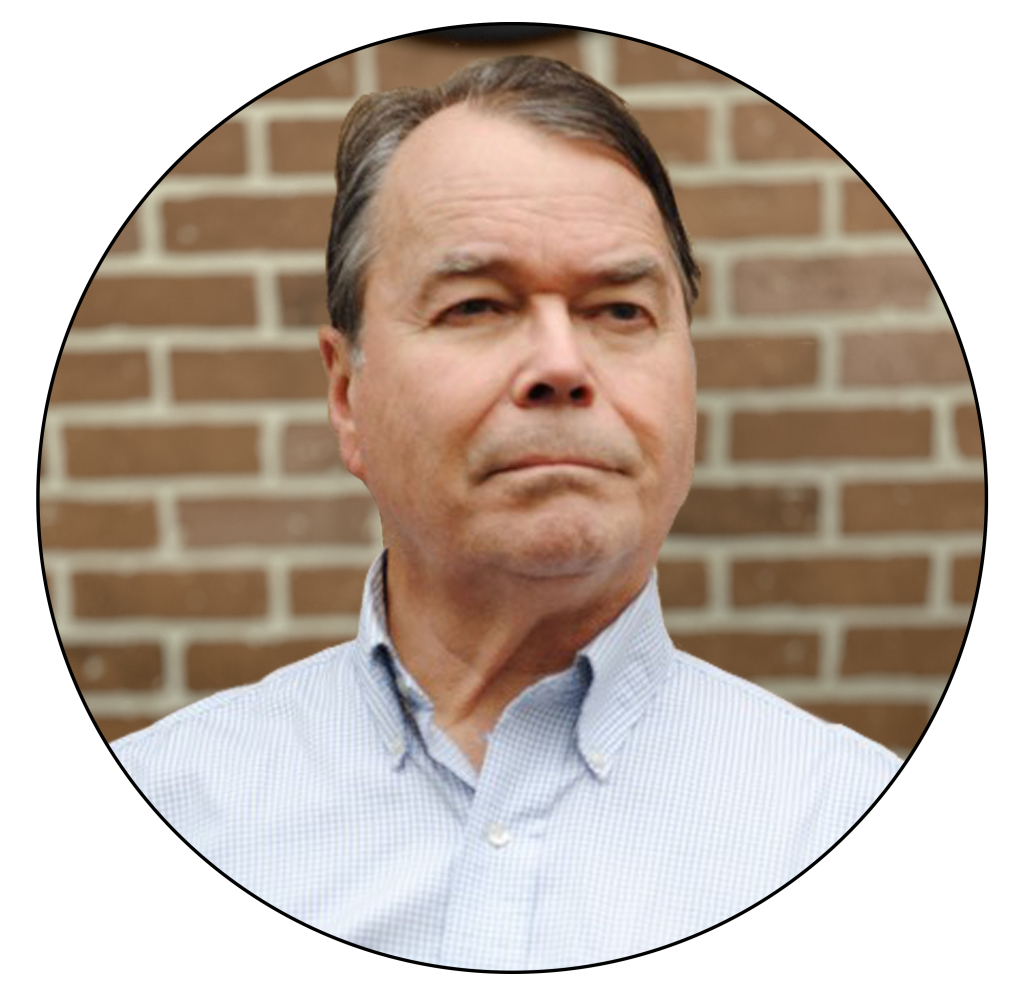
Written By
John Andrews
Director of Automation