- June 5, 2024
- Category: CQV
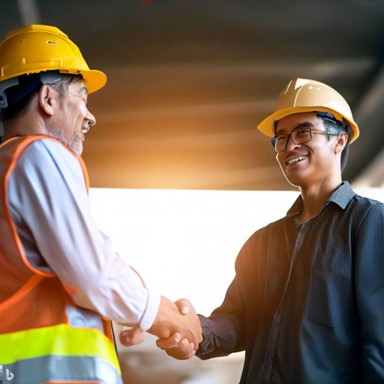
Commissioning, Qualification and Validation (CQV) and Construction Management (CM) share a symbiotic relationship that often defines the success or failure of projects in today’s fast-paced project environment. A mutually beneficial relationship between these two parties is a critical factor in ensuring project success, enhancing the client experience, and promoting best industry practices. This whitepaper explores how CQV and CM can operate in harmony to foster the successful delivery of projects, highlighting the role of systematic turnover, agreement on Mechanical Completion (MC) and the necessity of effective and accurate documentation.
Ensure clear definition on how turnover is to be managed with CM. An example of what not to accept from the CM is, “We’ll tell you when the system is done and send you the documents.” Turnover must be formal for commissioning and contractual reasons and must be a process that each party agrees to, with documented expectations and responsibilities.
The first step is to define Mechanical Completion (MC) and getting all parties to agree on the terms. This sounds obvious but the devil is in the details. Typically, MC = the completion of both the physical installation + the pre-determined documentation. It is common to hear, “The system is complete, just some paperwork left, and 50 punch items. Don’t worry, we’ll get you that ASAP.” Then, the documents never show up, or take months. If critical documents are not provided, then the CQV team is stuck with a system that can’t pass IV / IQ and the client either has to accept it with these deviations or get CM involved to possibly re-install/re-test. There have been times with perfectly good components removed and identical ones re-installed because the originals didn’t have the required critical documents. This is not a good situation for all parties – CM, CQV, PM, and the client. Author’s note – CM will sometimes push back on the idea that the definition of MC includes the documentation but my response is, “Yes, all the components are there and it matches the P&ID, but how do I know it was installed correctly without the testing documentation?”. For example, continuity checks prove the cabling has been verified as installed correctly, and this is part of CM’s scope.
The system must be accepted by CQV (and typically the client unless CQV is acting as a client proxy). It is a mistake to leave CQV out of the approval process for turnover as it can result in incomplete systems being accepted and delays in the CQV Phase. There is pressure to meet the schedule and move on to the next phase which is why this happens without CQV in the loop, but this is “kicking the can down the road” and it will result in even longer delays. CM’s motivation to fix a problem with a system that has already been accepted is much less than one that is still in their ownership.
OK, so how does CQV help CM be successful (and therefore help CQV)?
- Early alignment between CM & CQV, on WHAT documents are needed in TOP, HOW the TOP is to be structured, and WHEN the TOP is to be provided. It’s beneficial for CQV to be involved during the RFP stage, to review the RFP Bid Packages and vendor proposals (including CM and equipment vendors), to ensure their CQV / TOP scopes are properly contracted
- Testing documents – Make sure each contractor/subcontractor understands what is required of them, by craft: Electrical, Mechanical, Piping, etc. This will depend on the experience and quality of the contractor and their labor. We have had instances it was beneficial to provide training not only on Good Documentation Practices (GDP) but also on how to fill out the actual test sheets. This is not normally CQV scope but when the documents aren’t acceptable then something must be done. The first step should always be to discuss this with the CM, however.
- CM should have a documentation quality manager/lead (single point of contact), depending upon size of the project, this could be one person (dedicated or part time) or a team. The task shall be to assemble TOPs as the project progresses, such that these are not an afterthought. They understand what is needed to be acceptable and which documents are critical. Sidenote: an experienced CM will require this from each of their subs as well.
- CQV should review the test sheets as the subs are completing them, not wait until everything is finished. This avoids issues at turnover by providing a way to give feedback to allow corrections early in the process. Some CMs/subs don’t like this practice, even though it ultimately benefits them, so it should be specified in the contracts. This also helps ensure that documentation can be leveraged and therefore testing can be limited, where applicable, during CQV.
- Walkdowns – The normal process for verifying the physical portion of MC is via walkdowns. The CM will set a schedule of when systems will be ready to be verified and send out invitations. At a minimum, the invitees should include the client and CQV. The CM also prepares the drawings for the walkdown, which includes all redlines. Most systems just have one walkdown with the P&ID’s, however depending on the makeup of the system there may be more than just piping: electrical, controls, and mechanical (layouts). Sidenote: Don’t let the walkdowns become a “works to go” list for the CM. If more than a few incomplete items are found then this is an issue that needs to be brought up. Presenting systems for final walkdown that are not complete is an indication of poor CM execution.
- The CM should prepare their own internal pre-walkdowns, to reduce the quantity of punch items that are addressed, before the official MC walkdown occurs.
By embracing these best practices, CM and CQV can better collaborate toward the combined goal of project success. The key lies in understanding the shared responsibilities and integrating best industry practices in every step of the process, which ultimately leads to more effective project execution and a satisfied client.